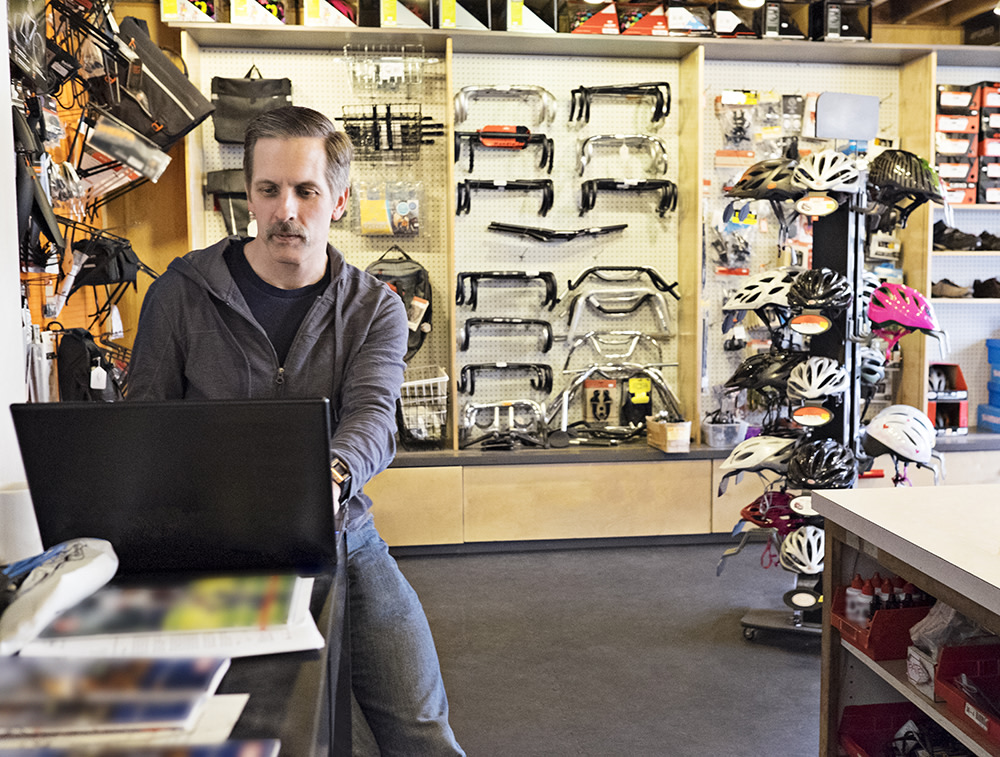
Meet manufacturing compliance management demands with NAVEX One
Proactively manage your manufacturing company’s risk with GRC solutions that cover supply chain, GMP compliance management, and OSHA, FCPA and more.
Manufacturing regulatory compliance refers to the adherence to laws, regulations, standards, and guidelines set by governmental authorities and industry bodies within the manufacturing sector (such as the FCPA, OSHA and GMP compliance management). These regulations ensure that products are manufactured safely and consistently and meet specific quality standards. Compliance with these regulations is essential for manufacturers to operate legally, maintain product quality, protect consumer safety, and minimize environmental impact.
In the intricate landscape of manufacturing, adherence to regulatory standards and risk management practices is paramount. Here are some key considerations:
Unpacking the challenges of risk and compliance in manufacturing
Navigating challenges within the realm of risk and compliance in the manufacturing industry demands a strategic approach. Here’s a breakdown of common hurdles:
Cultivating a unified understanding among teams
Manufacturing companies with dispersed operations and intricate processes struggle to ensure compliance with regulations. Neglecting essential employee and stakeholder training can lead to non-compliance or unethical practices, exposing the organization to reputational and financial consequences.
Elevating documentation practices beyond mere compliance
Insufficient documentation poses a significant risk of non-compliance and undermines the organization’s ability to demonstrate adherence to regulatory standards. Inadequate records may lead to mishandling of policies, ultimately jeopardizing the integrity of the compliance framework.
Ensuring whistleblowing compliance
With manufacturing companies often have a wide-spread workforce over multiple locations, it is essential to ensure employees can raise concerns about culture, bribery, cyber risks or non-ethical business practices. Without a well-communicated whistleblowing process in place, reports and cases may leak externally.
Use Cases
NAVEX's integrated ethics & compliance solutions help you prevent or address Environment, Health and Safety (EH&S) issues.
Get the use case
Datasheets
Integrate risk management to drive quality, innovate and compete globally using the Lockpath Platform.
Get the datasheet
Use Cases
Extend your ethics and compliance efforts to third parties.
Get the use case
Ensuring your company remains compliant can have many benefits:
Manufacturing risk and compliance essentials
Start your journey to strengthen manufacturing compliance risk management with these essential steps.
Establish a comprehensive code of conduct
Develop and implement a Code of Conduct that outlines the organization’s values, core policies, and expected behaviors for all stakeholders, including employees, executives, board members, and third parties. This code should serve as the foundation for ethical conduct throughout the organization, fostering a culture of integrity and respect.
Implement role-specific training programs
Utilize a scalable ethics and compliance training solution to provide role-specific training that aligns individuals with the organization’s values and compliance requirements. This training should be strategically designed to address specific risks and regulatory obligations relevant to each role within the manufacturing process, ensuring that employees are equipped to make ethical decisions and mitigate risks effectively.
Conduct regular risk assessments
Perform comprehensive risk assessments to identify and evaluate potential risks inherent in the manufacturing process, considering industry standards, regulatory requirements, geographical factors, third-party relationships, and other relevant variables. By systematically assessing risks, organizations can proactively identify areas of vulnerability and implement targeted mitigation strategies to minimize exposure to compliance breaches and operational disruptions.
Establish an effective reporting mechanism
Implement an open and anonymous hotline and incident management system to encourage stakeholders, including employees, third-party vendors, and other relevant parties, to report ethics and compliance violations without fear of retaliation. This reporting mechanism should enable timely identification and investigation of potential issues, allowing organizations to address concerns promptly and prevent recurrence. Additionally, administrators should regularly analyze reporting trends to identify emerging risks and implement corrective actions as necessary.
Leverage automation for policy management and third-party risk
Deploy automated solutions for policy management and third-party risk management to streamline compliance processes and enhance operational efficiency. These solutions enable the centralized creation, management, and distribution of critical policies across the organization, ensuring alignment with regulatory requirements and facilitating stakeholder attestation and auditability. Additionally, automated tools can facilitate the onboarding, screening, monitoring, and administration of third-party engagements, enabling organizations to manage risks associated with external partners and vendors effectively.
Discover the NAVEX products that can help you throughout your governance, risk and compliance journey.
Centrally manage your entire policy and procedure lifecycle.
Learn more
Ensure regulatory compliance, engage your people and build trust in your reputation with NAVEX reporting and whistleblowing solutions.
Learn more
Educate and engage your people with online training that speaks in their language, to their experiences.
Learn more
Easily identify third parties that share your vision and safeguard your most valuable partnerships with NAVEX One.
Learn more
Quick to launch, quick to deliver – NAVEX IRM out-of-the-box is your express route to mastering vendor risk management.
Learn more
Risk in the manufacturing industry refers to the possibility of encountering adverse outcomes or events that can impact production processes, product quality, safety or profitability.
Manufacturer compliance refers to adhering to various regulations, standards and guidelines set by authorities, industry associations, or customers to ensure products are manufactured safely, ethically and by legal requirements.
The three types of compliance are production compliance, OEM (Original Equipment Manufacturer), and product regulatory compliance.
Production compliance involves meeting standards and specifications throughout manufacturing to ensure products are produced consistently and meet quality requirements.
OEM compliance involves meeting the requirements and standards set by the original equipment manufacturer when producing components or products for them.
Product regulatory compliance involves ensuring products meet all the relevant regulations, standards and guidelines set by governmental bodies or industry authorities to ensure safety, quality and environmental responsibility.
A certificate of compliance is a document issued by a manufacturer or a third-party certifying agency to confirm a product, process or system meets specified requirements, standards or regulations.
Operational risk in manufacturing refers to the potential for disruptions, losses or failures within the manufacturing process due to factors such as equipment breakdowns, supply chain interruptions, or human error.
An example of a production risk could be equipment malfunction leading to unexpected downtime, disrupting production schedules and resulting in delayed deliveries or increased costs.
Risk analysis in manufacturing involves identifying, assessing and mitigating potential risks within the manufacturing process or supply chain to minimize the likelihood and impact of adverse events on operations, quality and profitability.